
the next generation of environmentally friendly cleaning solutions is here.



Let Our Business Take Your Business to Higher Grounds
With the emergence of laser technology, cleaning various substates have become easier, safer and more ecologically friendly. Let our dedicated team of experts assist your business in finding a solution that not only benefits your company, but the environment as well.
​
Leveraging Green
Subsidies
​
In the U.S., nearly half a billion dollars of government subsidies are available for switching to green and clean manufacturing technology. The Inflation Reduction Act of 2022 would create an additional $40 billion in clean manufacturing tax credits.
As a green technology, laser cleaning might give you access to government subsidies by reducing waste, energy usage, and harmful chemicals.
Laser cleaning replaces other polluting technologies that heavily rely on consumables such as chemical cleaning and sandblasting. Here are examples of common problems:
-
Some chemical processes use strong products and require proper rinse water disposal to prevent contamination.
-
With abrasive processes, the abrasive media gets mixed up with surface contaminants that are removed. Getting rid of this mixture in an environmentally friendly way can be complex and costly.
Manufacturers using laser systems do not have these concerns. Green benefits of laser cleaning include:
-
No consumables
-
No harmful chemicals
-
Zero toxic waste generated
-
Low-energy consumption
-
Long operating life
Proud to be the North American Distributor for

Our experts are ready to assist you on YOUR schedule
Call us to see how we can assist you in your cleaning needs. We can perform our services when production is shut down to keep your productivity at a maximum.
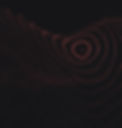
What are the advantages of laser cleaning?
Laser cleaning is a quiet, non-contact, non-abrasive, efficient, cost-effective, repeatable, high-precision and eco-friendly process that can be used to remove unwanted materials such as dirt, rust, paint, oil, oxides and other contaminants/impurities from surfaces.
The process, which can be used for micro-scale or large-scale cleaning of a number of materials, offers an attractive alternative to traditional industrial cleaning methods.
These can often be labour-intensive or require the use of consumables such as sand (sand-blasting techniques can also damage the underlying substrate) or hazardous chemical products/solvents (which then require costly disposal) depending on the material being removed. Laser cleaning on the other hand requires no consumables, only power, making it more environmentally friendly and cost-effective than such traditional methods.
How does laser cleaning work?
At its core laser cleaning involves an optical scanner being used to move a focused laser beam over a surface. Here the beam interacts with any unwanted material, which absorbs the energy and rises rapidly in temperature until its ablation threshold is reached – the point at which its molecular bonds break. This causes particulates of the material to be ejected away from the substrate, or for the material to be vapourised entirely.
The parameters of the laser beam – namely its power, wavelength, repetition rate, scanning speed and beam diameter – are carefully selected so that only the ablation threshold of the unwanted material is reached, rather than that of the substrate itself. This targeting of the right ablation threshold, combined with the fact that laser cleaning can be controlled with micrometre levels of precision, ensures that the underlying substrate is left completely free from damage.
The process can be conducted either in person, using a handheld system to move the scanning beam over the workpiece, or remotely, delivering the beam to a laser head via an optical fibre, which can then be moved over the workpiece automatically using robots within a safe enclosure.
To ensure user safety during laser cleaning, a suitable fume extraction system must be positioned next to the process to ensure that levels of harmful particulates that exceed the limits outlined by governments are not released into the air. Similarly, the user must also be protected in such a way that they are not being exposed to laser radiation levels that exceed the limits outlined by their government. The simplest, most effective way of ensuring user safety during laser cleaning is to have the application take place remotely, within a strictly controlled laser safety enclosure.
What substrates and contaminants can be cleaned using a laser?
Metals
Rust removal is one of the most common uses of laser cleaning, often done to ensure a clean, uncontaminted surface prior to welding or bonding applications. Rust removal is also performed to to restore metal products or structures, for example those with historic significance. The most common metals that can rust include iron, cast iron, wrought iron and steel.
For metals that don’t contain iron – and therefore do not rust – laser cleaning can be used on those that instead develop an unwanted oxide coating. Such coatings can influence the integrity of a product, and are a sign that its surface material is breaking down. However, removing the oxidation layer could expose it to further deterioration. This is where laser cleaning proves its advantage. Not only can it be used to remove the oxidation layer, but it can also remove any remaining contaminant oxides from the product, protecting it from further damage. The most common metals that form oxidation layers include common metals such as aluminium, bronze, brass and copper, as well as precious metals such as gold and platinum.
Similar to rust and oxides, the removal of grease, mould, dirt and paint is often done prior to metal welding or bonding to ensure a strong, contaminant-free bond. Thankfully laser cleaning is very capable of removing even the thickest layers of such unwanted coatings. With traditional cleaning methods, removing layers of chrome- or lead-based paints was previously a long, laborious and dangerous process. Lasers however can be used to safely remove such hazardous paints without creating additional waste.
Non-metals
As with metal cleaning, calibrated properly lasers can be used efficiently to ablate unwanted materials from ceramic surfaces without damaging the underlying substrate. Ceramic products frequently cleaned using lasers include print rollers, ceramic moulds, historical artefacts and baking moulds.
The flexibility of laser cleaning also makes it suited to removing grime and bacteria from natural stones such as marble, granite, limestone and concrete. In particular, the level of precision granted by laser cleaning makes it well-suited to cleaning extremely delicate stone objects, e.g. in the restoring of statues, figures, and ornaments, as well as larger surfaces such as building facades. Here, manual cleaning would have proven to be too abrasive, and could have damaged the substrates being cleaned.
While lasers are not as commonly used to clean plastics than the other-mentioned materials, they have been shown to be an effective solution for removing contaminants such as adhesion blockers from certain types of plastic. For example, polypropylene, acrylonitrile-butadiene-styrene copolymer, fibre-reinforced polyurethane and some carbon-fibre reinforced plastics (CFRPs) have all been cleaned successfully using lasers. For many other plastics, however, laser cleaning would likely not be suitable, as it would likely risk causing damage such as carbonisation or melting of the underlying substrate.
Similar to plastic, certain types of rubber have been cleaned successful using lasers. For example in the automotive industry lasers have been successfully used to clean the inside of tyres in order to bond sensors and other materials to them. However, also similar to plastic, the majority of rubber and elastomeric materials would likely not be as easily cleanable with a laser due the the ease at which they could be damaged. That’s not to say it isn’t impossible, but exceptional care (likely ensured via an automated, rather than handheld, laser cleaning solution) would be needed to achieve the extreme precision required to remove the surface contaminant without damaging the underlying substrate.
Technology that will
exceed your expectations, and results that insure your satisfaction.

We Take Pride in Our Numbers
18
Years of Experience
100+
Business Partners
136
Products Installed
2
Countries World Wide
5
Industry Awards
Our Partners

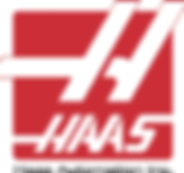

